Differentiating Quality LED strip light from cheap alternatives
- Genesis One Lighting
- Jan 17, 2023
- 4 min read
Updated: Apr 2
LED Strip can be a very controversial point of discussion especially when there are remarkable differences in prices for what is perceived to be the same thing. We are very often faced with contractors and clients who suggest that the LED strip can be bought from cheap retailers who will sell the product at a fraction of the price.
The one thing that is categorically clear is that the human eye cannot tell lumen output, nor can it determine the lux level that results from a specific light or light source. The human eye can determine light and dark, however it is a relative perception, because the eye compares the highest flux versus the lowest flux in a given area.

Today's discussion is to highlight the reasons why Quality LED strip light can be differentiated and the components and the considerations when procuring LED strips. Right from the outset the quality of LED strip is determined by many factors, many of which are often compromised to reduce the ultimate retail price.
Watch a video of LED STRIP MANUFACTURING HERE:
When considering the manufacturing process of quality LED strip light , it is critical to understand the use of quality raw materials. For example the PCB (printed circuit board) should be double layered, use pure copper material, should be flexible and bendable and have excellent heat dissipation. The resistors that are used on the PCB should be specialized for LED with an exceptionally low temperature drift, long soldering pins have flexibility and bendability. Further silicone glues are used in the manufacturing process, and these should have a high and low temperature resistance. They should be UV stabilized which prevents yellowing and should not become brittle.


In the manufacturing plants the storage environment for the raw materials becomes a critical factor in the longevity of the LED's. Precision electronic components should be stored in grounded containers on the floor ensuring an antistatic environment which will prevent any damage to the LEDs. Further strict temperature and humidity monitoring in the storage facility should be in place which should then be recorded and verified on an hourly basis.
When manufacturing the LEDs all the LED chips will go through a process of dehumidification for single colours. This process lasts for 24 hours. For the RGB LED chips the process lasts for 48 hours. The dehumidifying process is used to remove any air or vapour thereby removing any chance of colour change, dead LED chips or damage to the gold wiring caused by humidity.
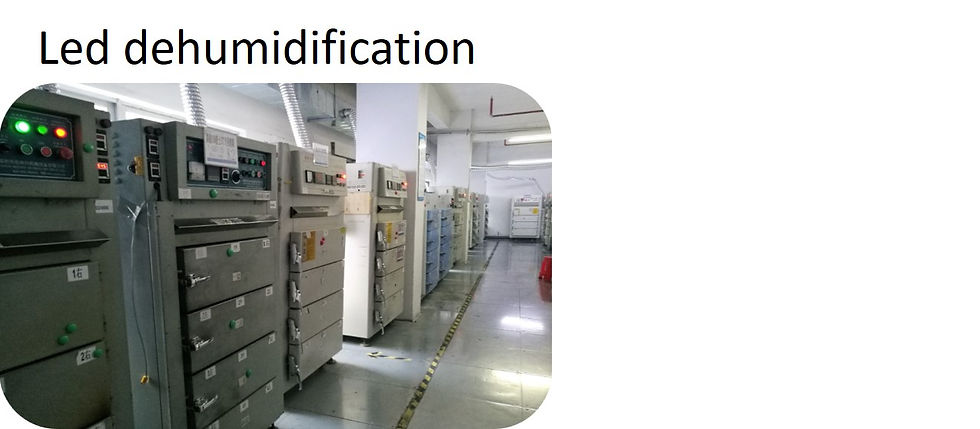
During the process of manufacture all the photometric parameters are verified and confirmed specifically CRI, CCT, wattage, current, and efficacy (LM/W).
One of the biggest problems in LED strip manufacturing has to do with faulty soldering. Poorly soldered LED Strip may pass the factory inspections however after the strip has been installed on site (which would be subject to being bent or twisted) the problems occur most frequently. It is therefore important to have excellent quality solder tin printing. This includes uniformity of the solder paste, the thickness of the solder paste and the flatness or smoothness of application of the solder paste. The solder paste must be stored in extremely strict conditions at specific temperatures to get the best results. All too often the manufacturing facilities do not pay attention to the solder paste which causes endless problems on site.
The next step in LED strip manufacturing has to do with surface mounting the LED chips. This is normally done using an SMT machine. LED's are precision mounted on the PC board according to a computer-based program. Once the LED's have passed through the SMT machine the mounted diodes are presented for visual inspection. Visual checking is done to confirm the colour consistency, the brightness and if there are any failed LED chips. During this visual inspection, the solder would be checked for false welding, short circuits, direction of the LED placement, leakage or deviation, or any overlapping.

A further area of complication has to do with the cable soldering onto the PCB once the LEDs have been placed correctly. The soldering on the welding joints would have a key impact on the lifespan of the LED strip. The LED soldering should not deviate by more than 0.24 mm and not have greater than 0.13 mm into space between the two PCBS after the stitch welding.
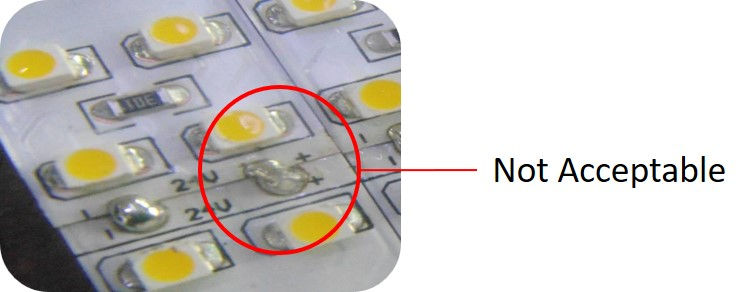
Once the LED's have successfully been placed on the PCB and all the visual tests have been done the stability control and various tests would be conducted to confirm the high and low temperature parameters, anti-static testing, full spectrum analysis, IEC photometric generation and the LM80 report. LEDs would be subject to a vibration test, drop test, UV test, anti-salt fog test, constant temperature and humidity testing as well as the waterproof grade testing.
LED Strip longevity Led’s often become subject to expectations that suggest that LED’s can burn 24hr/ day for the duration of the warranty and continue to the life hours stated on the data sheets. While there is every possibility that this may occur, certain considerations need to be taken into account. Led Strip is manufactured with a specific copper content that ranges on the low end of 0.25 ounces/ meter building up in increments up to 4 ounces of copper / meter. The professional LED strip will start on the lower end with 2 ounces copper / meter. It is highly recommended that if you have a project that requires a 24 hr burn, you ensure that you have 4 ounces of copper / meter to ensure longevity and the best possibility to prevent premature failure. Genesis One Lighting has a range of high-quality LED strip and profile along with the expertise to support your lighting project. Please feel free to contact us on sales@genesisone.co.za
Comments